Nabson (USA)
Development of power connectors
for the aerospace industry
Background
Nabson’s largest production activity is the manufacture of ground power cable assemblies and connectors for the commercial and defense aerospace industry.
In early 2019, Nabson purchased a dual-head FDM 3D printer to accelerate R&D for new products and the development of one of its product lines. Based on the success of the FDM printer, Nabson sought to expand its 3D printing capabilities in late 2019 with an SLS printer that could produce small parts and prototypes with higher accuracy.
After conducting extensive market research, they selected Lisa PRO to balance cost and capability.
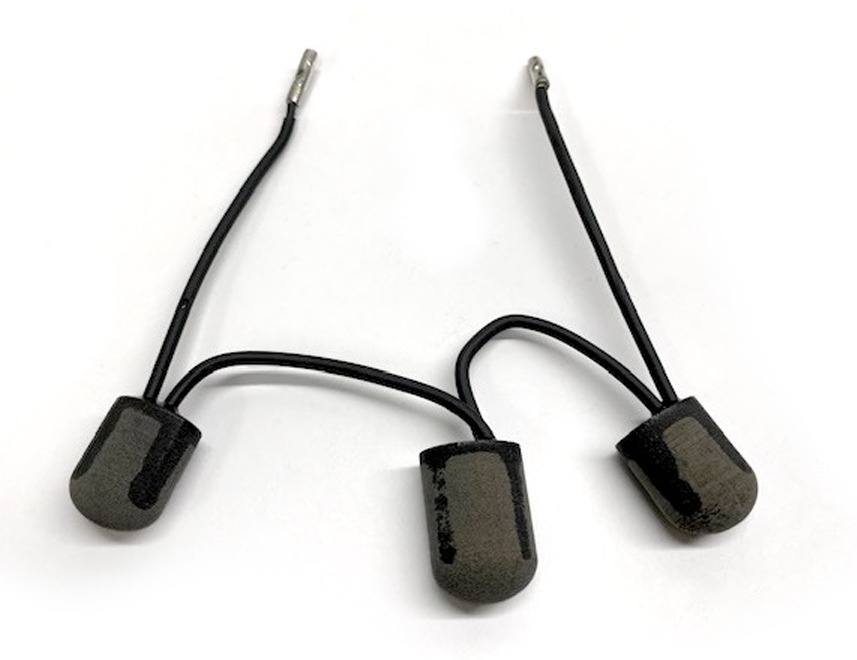
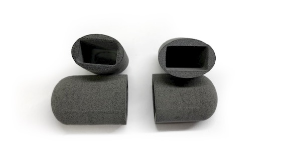
Problems
To improve safety in a particular product line, Nabson was asked to install a series of thermal switches that would shut off power to the aircraft if the connector overheated.
They had to solve two problems:
- The amount of free space in the rubber overmoulded connector is severely limited
- The thermal switches had to be coated with epoxy to protect them from the pressure exerted on the switches during the rubber injection process.
The engineers were tasked with working with the assembly team to develop a sleeve that, when filled with epoxy, would protect the thermal switch during the injection process and allow sufficient heat transfer to the switch itself.
Solution
Due to the size of the part, they decided to use Lisa PRO and produce the part in-house because the outsourcing costs were estimated to be almost double. In addition, they got the opportunity to continuously modify the design, which they ended up doing twice.
Lisa PRO provided the required accuracy, as the dimension of the thinnest wall in the corners was 0.6 mm. The team was given the opportunity to print three to four designs overnight, fill them with epoxy and test the results the same day.
Due to high demand, the Lisa PRO printer worked almost 7 days a week for several months without incident. More than 1500 sleeves were produced.